What Is Kaizen?
- Michael J Robey Psychic.gr
- Jul 25, 2018
- 6 min read
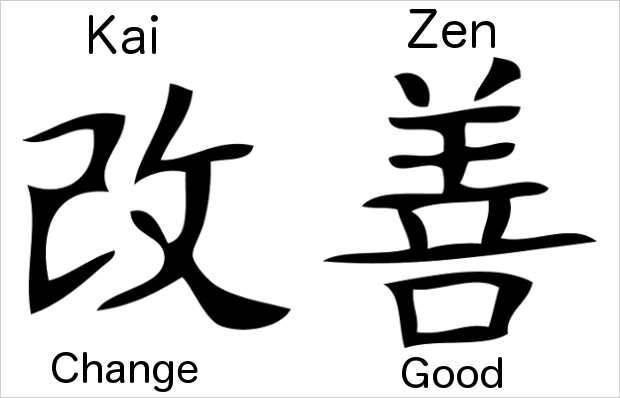
What Is Kaizen? Kaizen (改善), is the Japanese word for "improvement". In business, Kaizen refers to activities that continuously improve all functions and involve all employees from the CEO to the assembly line workers. It also applies to processes, such as purchasing and logistics, that cross organisational boundaries into the supply chain. It has also been applied in health care, psychotherapy, life-coaching, government, banking, and other industries. By improving standardised programmes and processes, Kaizen aims to eliminate waste (see lean manufacturing). The History of Kaizen Kaizen was first practised in Japanese businesses after the Second World War, influenced in part by American business and quality-management teachers, and most notably as part of "The Toyota Way". It has since spread throughout the world and has been applied to environments outside business and productivity. Kaizen, also known as continuous improvement, is a long-term approach to work that systematically seeks to achieve small, incremental changes in processes in order to improve efficiency and quality. Kaizen can be applied to any kind of work, but it is perhaps best known for being used in lean manufacturing and lean programming. If a work environment practises kaizen, continuous improvement is the responsibility of every worker, not just a selected few. Kaizen can be roughly translated from Japanese to mean "good change." The philosophy behind Kaizen is often credited to Dr. W. Edwards Deming. Dr. Demming was invited by Japanese industrial leaders and engineers to help rebuild Japan after World War II. He was honoured for his contributions by Emperor Hirohito and the Japanese Union of Scientists and Engineers. The Kaizen Philosophy Interestingly, Kaizen as an action plan is exactly what develops Kaizen as a philosophy. When Kaizen is applied as an action plan through a consistent and sustained program of successful Kaizen events, it teaches employees to think differently about their work. In other words, consistent application of Kaizen as an action plan creates tremendous long-term value by developing the culture that is needed for truly effective continuous improvement. In his book "Out of the Crisis," Dr. Deming shared his philosophy of continuous improvement: 1. Create constancy of purpose toward improvement of product and service, with the aim to become competitive and to stay in business and to provide jobs. 2. Adopt the new philosophy. 3. Eliminate the need for inspection on a mass basis by building quality into the product in the first place. 4. End the practise of awarding business on the basis of price tag. Instead, minimise total cost. Improve constantly and forever the system of production and service to improve quality and productivity and thus constantly decrease costs. 5. Institute training on the job. 6. Institute leadership. The aim of supervision should be to help people and machines and gadgets to do a better job. 7. Drive out fear so that everyone may work effectively for the company. 8. Break down barriers between departments. People in research, design, sales and production must work as a team to foresee problems of production and use of the product or service. 9. Eliminate asking for zero defects and new levels of productivity. Such exhortations only create adversarial relationships as the bulk of the causes of low quality and low productivity belong to the system and thus lie beyond the power of the work force. 10. Remove barriers that rob the hourly worker of his right to pride of workmanship. 11. Remove barriers that rob people in management and in engineering of their right to pride of workmanship. 12. Institute a vigorous program of education and self-improvement. 13. Put everybody in the company to work to accomplish the transformation. The transformation is everybody's job. A Kaizen Blitz In Western civilisation, Kaizen is often broken down into four steps: assess, plan, implement and evaluate. In Western workplaces, a "Kaizen Blitz" is synonymous with a concentrated effort to make quick changes that will help achieve a short-term goal. The Big Idea By creating a "Big Idea"culture of continuous improvement where all employees are actively engaged in improving the company, and nurturing this culture by organising events focused on improving specific areas of the company. Kaizen is a strategy of continuous Improvement where employees at all levels of a company work together proactively to achieve regular, incremental improvements to the manufacturing process. In a sense, it combines the collective talents within a company to create a powerful engine for improvement. The Dual Nature of Kaizen Kaizen is part action plan and part philosophy: As an action plan, Kaizen is about organising events focused on improving specific areas within the company. These events involve teams of employees at all levels, with an especially strong emphasis on involving plant floor employees. As a philosophy, Kaizen is about building a culture where all employees are actively engaged in suggesting and implementing improvements to the company. In truly lean companies, it becomes a natural way of thinking for both managers and plant floor employees. Kaizen works hand-in-hand with Standardised Work. Standardised Work captures the current best practises for a process, and Kaizen aims to find improvements for those processes. Note the emphasis on current; Standardised Work is living documentation (it continually evolves through Kaizen). A Kaizen Event A typical Kaizen event follows this pattern: Set goals and provide any necessary background. Review the current state and develop a plan for improvements. Implement improvements. Review and fix what doesn’t work. Report results and determine any follow-up items. This type of cycle is frequently referred to as PDCA (Plan, Do, Check, and Act). PDCA brings a scientific approach to making improvements: Plan (develop a hypothesis) Do (run experiment) Check (evaluate results) Act (refine your experiment; then start a new cycle)
Your Workplace In many workplaces across the world, there is little understanding of training in effective management, processes, philosophies, worker engagement in policy and procedures, etc. This leads to lack of management, structure, goals, direction, focus and success. Cultivating inefficiencies, communication breakdowns, and oppressive, hierarchical , compartmentalised, ineffective management, employer / employee divide, and poor outcomes. Your workplace may be the one place you spend most of your day. It is your means to secure your home and family indirectly. So cherish and nourish it.
The combination of the concentric whole as an efficient complex cog of inter dependent functions (just like a Swiss watch) -has a far greater power than the sum of individuals compartmentalised and divided with no direction or purpose. So take a look at your work place whatever position you may have in it and bring efficiency and harmony to it.
Applying Kaizen Principles To Your Personal Life
1.Seek Improvement - There is an area of improvement in everyone's life no matter how successful they are.
2. Eliminate Old Practises - Let go of former habits, even if they seemed to have benefited you in the past.
3. Be Proactive - Stop hesitating because of possible hurdles that you foresee, and move forward towards your goal.
4. Don't Assume New Methods Will Work - Just because something worked for someone else does not mean that it will necessarily work for you.
5. Make Corrections - Recognise the areas of you life that can use improvement, and make relevant corrections to help you progress.
6. Empower Others To Speak Up - Encourage your fellow workmates, employees, friends and family to make suggestions, if they see things that you could work on.
7. Crowd Source - Learn from other people and get some new ideas on things you can add to your routine to create continuous improvement.
8. Practise the *Five Why Method" - By continuing to ask yourself "why" you are likely to find the real reason behind a problem.
9. Be Economical - Consider specific things you can save money on each week, and stop buying them.
10. Don't Stop - Never consider yourself to be finished article, improvement has no limits and be continued on an infinite level.
Try to do something just a little bit each day in order to make a large impact in the long run. Always remember "The whole is greater than the sum of its parts"

Michael J Robey
Psychic Medium | Psychic Investigator
Psychic.gr
www.psychicgr.com
Try to do something just a little bit each day in order to make a large impact in the long run.
Comments